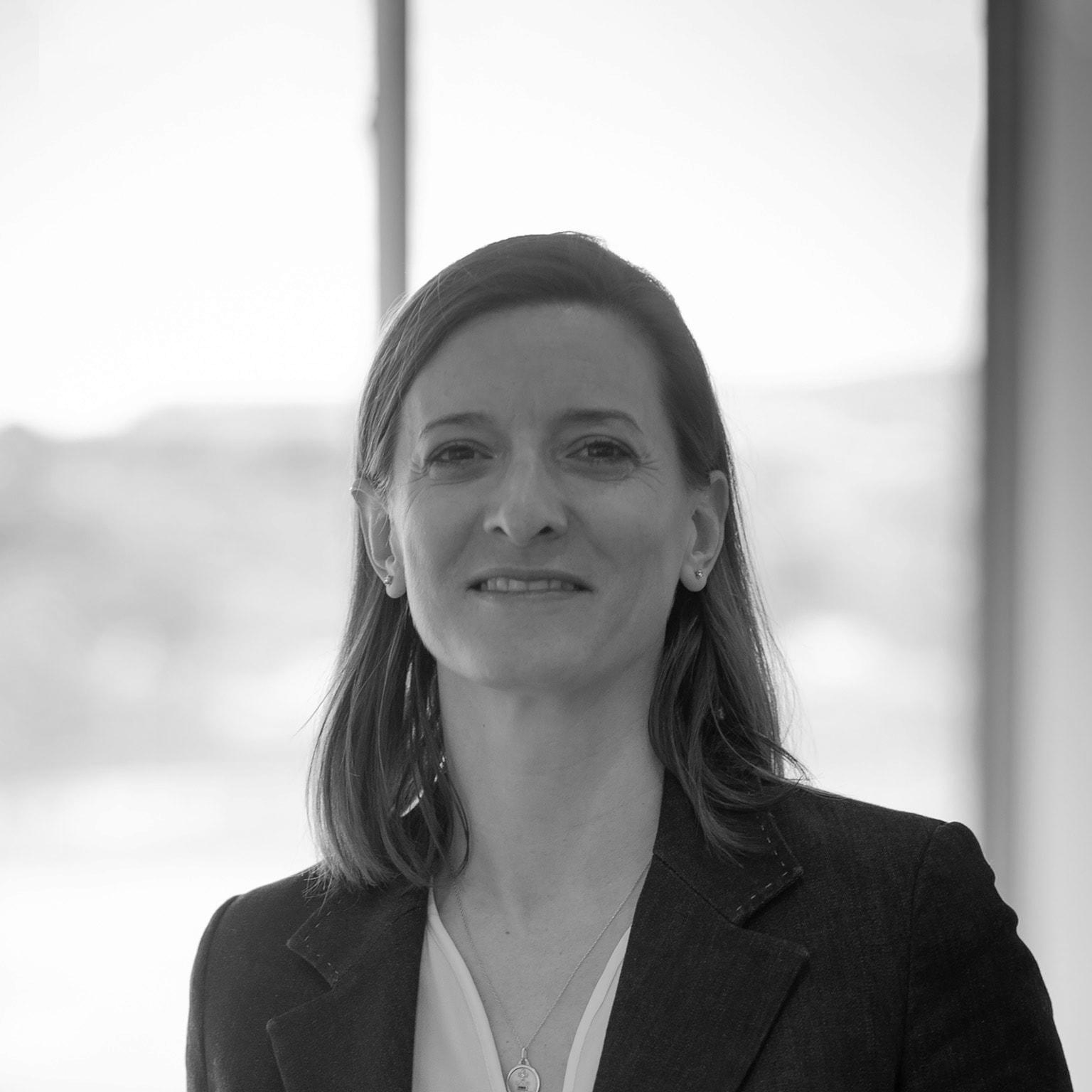
Aerospace OEMs are under pressure to ramp up production, improve operations, and increase sustainability, but multiple challenges persist. Supply chain issues are particularly acute, and a delay in shipping a single component often creates a domino effect that ripples through the production process. While tackling these problems can be challenging, some aerospace companies have been able to mitigate or overcome long-standing obstacles by implementing digital solutions. McKinsey partner François Soubien recently spoke with Delphine Bazaud, senior vice president and head of industrial supply chain and digital operations at Airbus, to discuss some of her company’s most innovative digitalization initiatives. An edited transcript of the conversation follows.
François Soubien: Before getting into digital solutions, can you tell me about production levels at Airbus?
Delphine Bazaud: Before the COVID-19 crisis, Airbus was ramping up production, mainly for the single-aisle family for the A320 program. During the pandemic and the aftermath, production slowed down, but now we’re very close to the production levels we had before COVID-19.
Now we are ramping up again. What makes this phase special is that we are ramping up not only single-aisle families—A320 and A321—but also our other programs, including A220 and wide-bodies such as the A330 and A350 programs. In order to support that growth, we are expanding our capacity in Europe and even overseas in China and the United States.
We have a very high investment in new lines and all production sites for Airbus. It’s not just about the facilities or industrial capabilities. The ramp-up is also about people and making sure we have the right number of employees with the right skills.
Ramp-up also requires attention to our ecosystem. We know our supply chain suffered during the COVID-19 crisis, and we must support our suppliers by working together. That’s what makes this challenge very exciting. We have to make sure everything is covered.
François Soubien: Related to that question, can you ballpark the investment you’re making along the value chain to improve operations?
Delphine Bazaud: We invest several billion every year in new capacity, including warehouses and production lines. We’re also investing in automation to reach the next level of production. The investments are designed to increase our production efficiency as we’re growing.
François Soubien: What insights have you uncovered as you have applied digital solutions to aircraft that have a complex production process?
Delphine Bazaud: We’ve been investing in digitalization for decades and learned a lot about possible solutions for different parts of our business: engineering, sales, operations, quality, manufacturing, and logistics, among others. Now we need to rationalize because some solutions overlap or do not use the same data source. We need to focus on a limited number of solutions that are based on accurate, complete, and quantitative data.
François Soubien: What internal and external investments has Airbus made in digitalization?
Delphine Bazaud: Internally, we have invested a lot in data and data quality. This is probably less exciting than developing new solutions, but it’s a key element that is necessary to ensure that we speak the same language and that, for example, we don’t have three or four different ways to analyze missing parts. We have four different single-aisle final assembly lines in Germany, France, China, and the United States, so we need to have a standard way to measure the same key performance indicators.
Of course, we need to extend our approach to our supply chain and build the right framework to share reliable information. We already have existing tools to share demand information, but we want to take it to the next level and share more data with not only tier-one suppliers but those in tiers two and three to solve some pain points. Some of our priority use cases relate to quality issues and how to follow up with our suppliers.
François Soubien: If we consider the number of parts that go into each aircraft in all locations, as well as the multiplicities of flows and suppliers, we are talking about millions of parts. Will you need to rebalance your investment in digital solutions to achieve the transparency you need?
Delphine Bazaud: Yes, that’s one of the challenges we are facing at the moment. We have invested in our transactional execution system for the past two decades. We still have multiple SAP platforms; we’d like to harmonize these and eliminate some.
This takes time, and it does not just involve IT. To be able to deploy the same harmonized solution, you need to have harmonized processes across the board. So now the question is this: Can we leverage data and analytics to make other improvements now and perhaps slow down harmonization of transactional systems? We are trying to find the right balance.
François Soubien: AI technologies are developing very quickly, starting with generative AI [gen AI]. Within your portfolio of applications, what practical applications or use cases have you identified for this technology?
Delphine Bazaud: We are definitely moving from using analytics to measure things that already exist, such as missing parts, and moving toward using them for prediction. How can we estimate future missing-part levels using information from our suppliers in combination with other data coming out of recent events and past experience?
For out-of-sequence work, we are applying the same philosophy. Rather than just measuring the level of out-of-sequence work, we are using digital tools to estimate what type of out-of-sequence work will have the greatest impact later in production. This will allow us to prioritize and address the right topics before they create bottlenecks. By moving from measurement to prediction, we can make the right decisions at the right point.
François Soubien: How many digital initiatives are now under way at Airbus, and what impact do you think they will have?
Delphine Bazaud: We have hundreds of initiatives that involve data and analytics. Now we must take them to the next level by using AI to create even more value. For that, I believe we need a mindset change. If I can make a parallel with production: when you want to produce parts through 3D printing rather than standard production, you might not get a positive business case if the engineering teams don’t design the part with 3D-printing capabilities in mind. It’s the same for digital solutions at companies that are not digital natives. We need to upskill and to be able to think, “What can we get from AI or gen AI if we build them into the solutions we are developing?”
François Soubien: Do you think digital solutions could help reduce Scope 1 and 2 emissions?
Delphine Bazaud: To comply with Corporate Sustainability Reporting Directive requirements for emissions, we must measure and report on more than 200 data points, so we will need digital capabilities to support that journey. If you look at our Scope 1 and 2 emissions, transportation accounts for 30 percent of the total, so we must optimize and decarbonize transport activities.
One of my favorite projects involves Europe-to-US transportation flows. We announced last year that we will purchase three vessels. The first, which goes into service in 2026, will have a new propulsion system with six Flettner rotors that will use wind power, as well as a dual-fuel engine that will be able to run on e-methanol. It will also be equipped with software that will optimize the boat’s route to maximize the use of wind propulsion to reduce fuel consumption further. I think this is a good example of how we can combine hardware and software to support the reduction of Scope 1 and 2 CO2 emissions.
François Soubien: Beyond improving sustainability, what are some of your major goals for digital operations at Airbus over the next few years?
Delphine Bazaud: I’d like to find the right balance between centrally developing harmonized tools that are deployed across the board and leaving room for local innovation—small, very specific solutions to address a specific pain point. Finding that balance is probably one of the trickiest challenges today, but it will help us demonstrate how digital can bring added value to industrial systems.
“Our firm is designed to operate as one—a single global partnership united by a strong set of values. We are equally committed to both sides of our mission: attracting and developing a talented and diverse group of colleagues and helping our clients create meaningful and lasting change.
From the C-suite to the front line, we partner with clients to help them innovate more sustainably, achieve lasting gains in performance, and build workforces that will thrive for this generation and the next.”
Please visit the firm link to site